1 阀体零件去毛刺的重要意义
去毛刺技术是阀体零件光整加工的重要组成部分,也是阀体零件生产的*终精加工工艺,它的发展水平直接关系到产品的质量和性能,以及产品的成本和价格。国外已从系统工程角度来对待去毛刺问题,提出了“毛刺工程”(BurrEngineering),例如美国平均每年花在**零件上毛刺的费用都在20亿美元以上。一般来讲去毛刺工序会使阀体零件的制造成本增加10%~20%。目前多采用刮刀、油石、砂布、钢丝刷轮等手工、机械的方式去毛刺,费工费时,劳动强度大又污染环境,不符合绿色产品的要求,而且只能靠目测感觉操作,去毛刺质量难以保证。由于阀体零件内腔的交叉孔处、环槽等部位的毛刺去除的不彻底。一则导致气体或液体的流阻增加,二则还会划伤阀芯上的密封圈,严重影响产品性能及使用寿命。如果残留的毛刺在机器振动及高压气流或液流的冲击下,脱落掉入工作系统中,其后果更不堪设想。为此大大促进了去毛刺技术的研究与开发。
2 阀体零件电化学去毛刺工艺研究
苏州长风电化学去毛刺技术是由电解加工发展而来的一项新工艺,只要正确的选择电解液配方、合理的设计工具阴极及流场,便可发挥电解加工的优越性,成功地去除用机械方法不易去掉的毛刺,并且具有良好的表面质量。通过阳极溶解,既使尖角棱边倒圆角,又可去除加工表面的变质层,改善加工表面的物理、化学、机械性能。并且100%去除加工部位的毛刺,确保零件的加工质量及产品的工作可靠性。尤其适用于阀体零件内腔中的环槽、交叉孔端的毛刺去除。我们针对某阀体内腔多个垂直交叉孔端去毛刺并倒圆角R0.2,其表面粗糙度达到Ra0.8μm的要求,在利用单电极工艺试验及数据分析的基础上,研制出该阀体零件电化学去毛刺夹具,由于阀体内腔。山东省教委资助项目中的几个垂直交叉孔中各有一个工具电极,则使毛刺去除的彻底、均匀、光滑,加工效率提高5~10倍;另外基于从每个加工孔中的工具电极加工状态采样处理而研制的DMC-1型电化学去毛刺加工状态监测仪,可同时采集16个孔的加工数据,因此可适时检测每个孔去毛刺的加工状态即倒圆角是否达到R0.2要求。图1为电化学去毛刺加工原理示意图。由黄铜制作的管状工具电极(阴极),其外表面涂环氧树脂绝缘层(厚度为0.2mm~0.4mm),但对应于工件(阳级)去毛刺部位的绝缘层被剥除,并沿圆周钻有数个小孔(0.6~0.8),以便电解液(10%NaNO3)流出。进入阴、阳极形成的加工间隙(0.4mm~0.6mm)中。在直流电场作用下,随着阳极溶解,工件表面上生成钝化膜,而锐边毛刺部位由于突出于工件表面,受电场、温度场及流场的影响,加速了离子的扩散与迁移,难以形成钝化膜,且突出的毛刺部位电流密度又很大,于是锐边毛刺首先被溶解并形成圆角R。
3 去毛刺加工状态即倒圆角R的监测研究
圆角R的大小取决于电流I和时间t。分流器采用大功率小电阻,由PLC经A/D转换,可连续检测去毛刺过程加工电流随时间的变化规律。电化学去毛刺加工状态监测仪测得的阀体零件内腔交叉孔端去毛刺过程典型的电流随时间连续变化曲线。去毛刺过程的前10秒内,电流变化波动幅度较大,这说明毛刺原始状态不规则,10s以后电流趋于稳定,说明毛刺已去除并形成圆角R,再以后随着时间加长,只是圆角R增大而已。
4 结束语
阀体零件采用苏州长风电化学去毛刺机及其监测技术,可确保去毛刺的质量,使毛刺去除的均匀、彻底、光滑,并且能实时检测各毛刺部位去除过程的加工状态即倒圆角是否达到要求。进一步扩大了电化学去毛刺在光整加工领域中的应用,并为去毛刺倒角实施定量分析和控制开辟了新路。
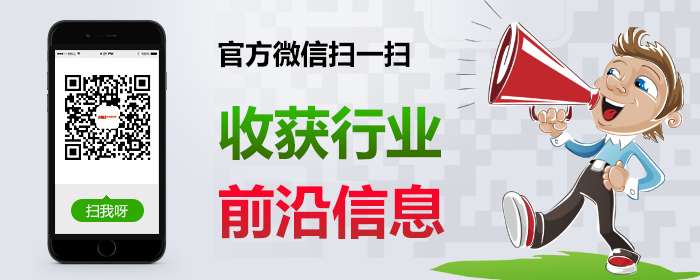